DESCRIPTION
LY-4450 rigid filling foam system is a two part polyurethane system comprises a polyol and isocyanate component..When mixed in their correct proportions produce a fine-celled foam with a free rise density, 450±50 kg/m3.
The system is designed for use in moulding applications where good skin is required. The foam can be used for moulding components such as imitation wood and cavity casting.
The system can be manually drill mixed (@ a minimum speed 2000 rpm) however it is best
processed through high-pressure plural polyurethane dispensing equipment.
COMPONENT PROPERTIES
REACTION PROFILE
Laboratory results based on hand-mix @ 20°C
Mix ratio by weight (Polyol: Iso=1:1)
FOAM PERFORMANCE
STORAGE CONDITIONS AND HANDLING
The components are sensitive to humidity and should at all times be stored in sealed drums. The recommended storage temperatures are 18-25 C, which will give a normal shelf life of 6 months.At elevated temperatures problems may arise with pressure build-up within the drums. When opening these drums extreme care must be exercised in releasing the internal pressure. It is recommended that the drum contents should be mixed well before use.
HEALTH AND PERSONAL PROTECTION
Before handling these chemicals please consult the Material Safety Data Sheets for the two
components. The polyol component contains tertiary amines. Contact with the skin or eyes must be avoided. Safety goggles and protective gloves should be worn whenever handling both of the chemicals. Splashes that come into contact with the skin must be wiped off immediately and the contaminated area washed with soap and water. Splashes in the eye must be flushed immediately with plenty of clean running water. If irritation occurs thereafter contact an eye specialist.
GENERAL INFORMATION
At temperatures less than 15 C the reaction rate of Erathane MF115 will be much slower resulting in an increase in density, and reduction in foam yield. Also at temperatures above 30 C the cream time will be drastically reduced.
LY-4450 rigid filling foam system is a two part polyurethane system comprises a polyol and isocyanate component..When mixed in their correct proportions produce a fine-celled foam with a free rise density, 450±50 kg/m3.
The system is designed for use in moulding applications where good skin is required. The foam can be used for moulding components such as imitation wood and cavity casting.
The system can be manually drill mixed (@ a minimum speed 2000 rpm) however it is best
processed through high-pressure plural polyurethane dispensing equipment.
COMPONENT PROPERTIES
Item | POLYOL | ISOCYANATE |
Apperance | Clear amber liquid | Dark brown viscous liquid |
Viscosity@25ºC,cps | 500±100 | 150-250 |
Specific gravity@20ºC, mPa.S | 1.05±0.02 | 1.26-1.25 |
OH content, mgKOH/g | 350±50 | |
NCO, % | 30-32 |
REACTION PROFILE
Laboratory results based on hand-mix @ 20°C
Mix ratio by weight (Polyol: Iso=1:1)
FOAM PERFORMANCE
ITEM | PROPERTY |
Moulded Density,kg/M3 | 500-1000 |
Compressive strength,Mpa | 10-20 |
Surface strength,Shore A | 70±5 |
Cohesiveness/Adhesion Strength | well |
STORAGE CONDITIONS AND HANDLING
The components are sensitive to humidity and should at all times be stored in sealed drums. The recommended storage temperatures are 18-25 C, which will give a normal shelf life of 6 months.At elevated temperatures problems may arise with pressure build-up within the drums. When opening these drums extreme care must be exercised in releasing the internal pressure. It is recommended that the drum contents should be mixed well before use.
HEALTH AND PERSONAL PROTECTION
Before handling these chemicals please consult the Material Safety Data Sheets for the two
components. The polyol component contains tertiary amines. Contact with the skin or eyes must be avoided. Safety goggles and protective gloves should be worn whenever handling both of the chemicals. Splashes that come into contact with the skin must be wiped off immediately and the contaminated area washed with soap and water. Splashes in the eye must be flushed immediately with plenty of clean running water. If irritation occurs thereafter contact an eye specialist.
GENERAL INFORMATION
At temperatures less than 15 C the reaction rate of Erathane MF115 will be much slower resulting in an increase in density, and reduction in foam yield. Also at temperatures above 30 C the cream time will be drastically reduced.
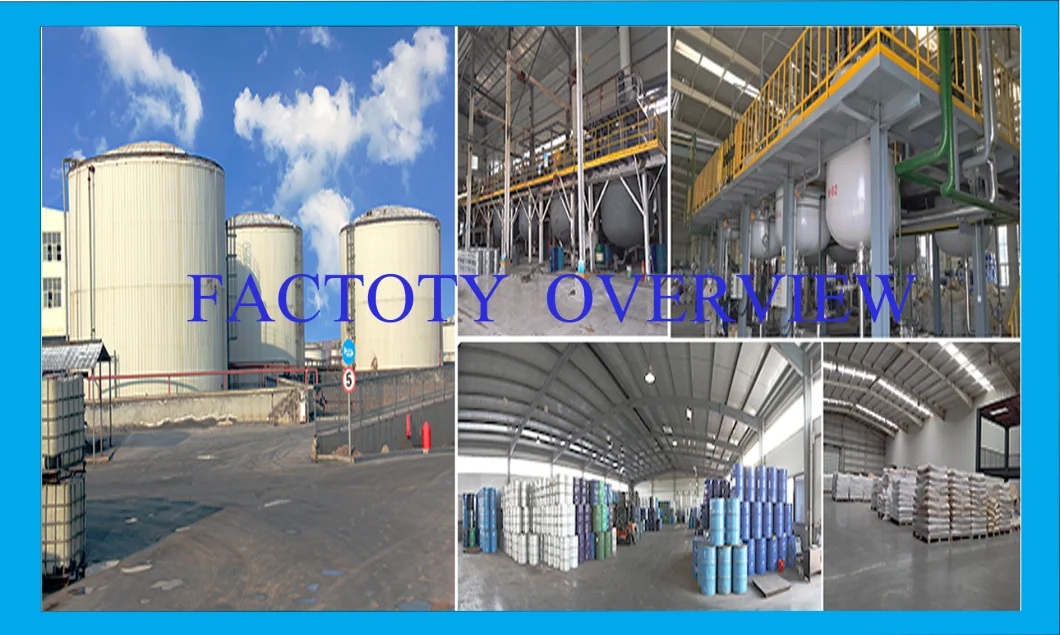
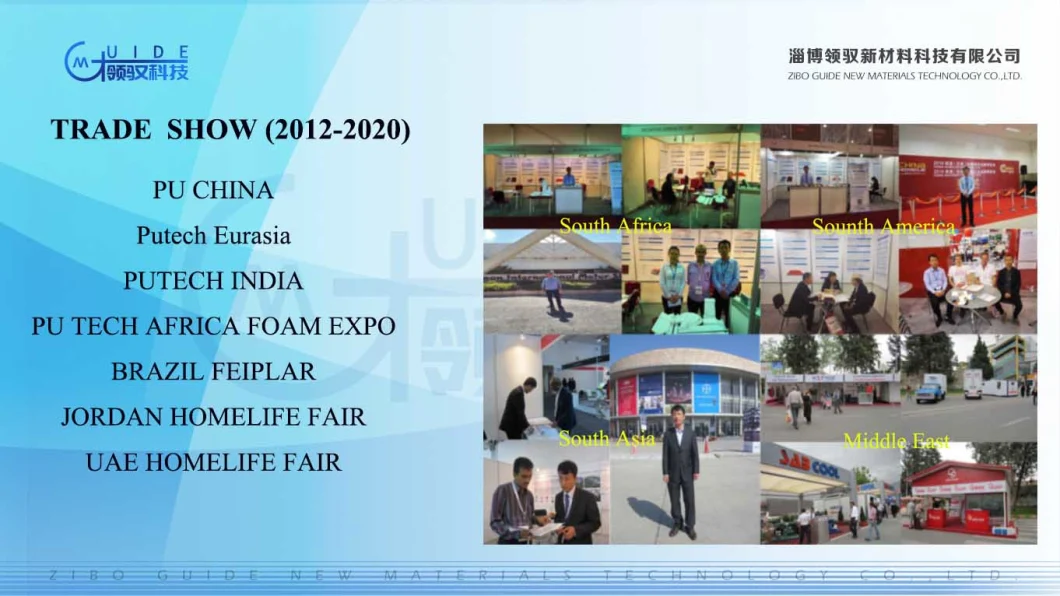
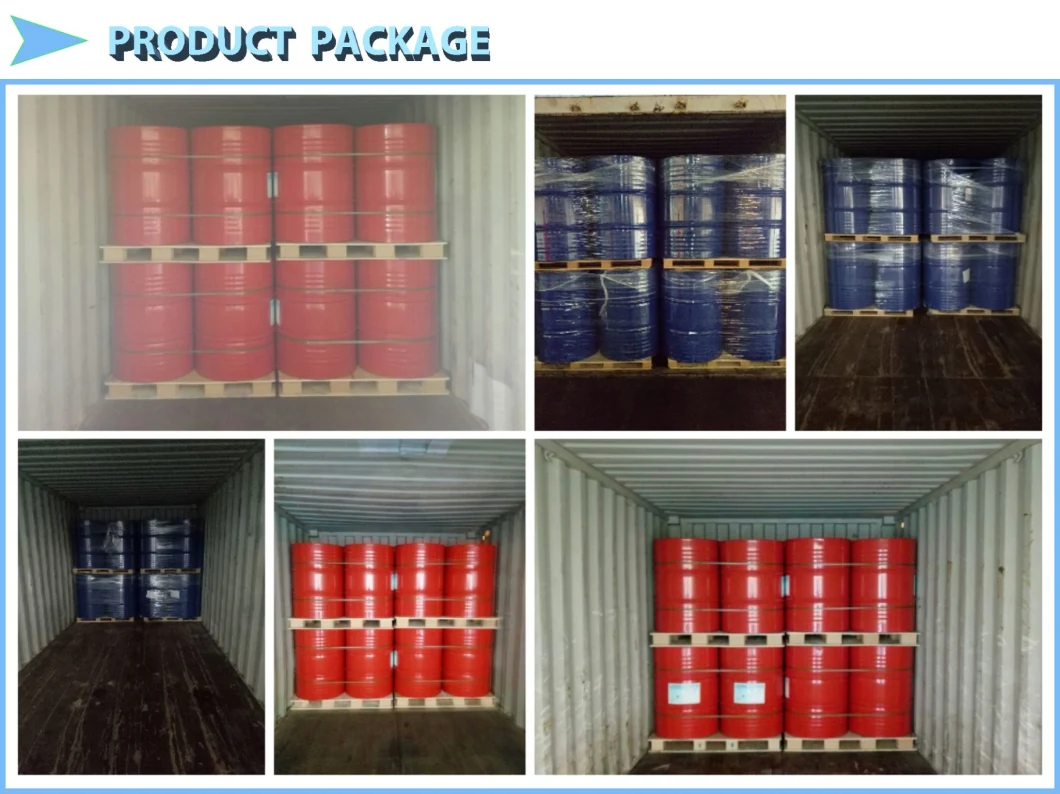
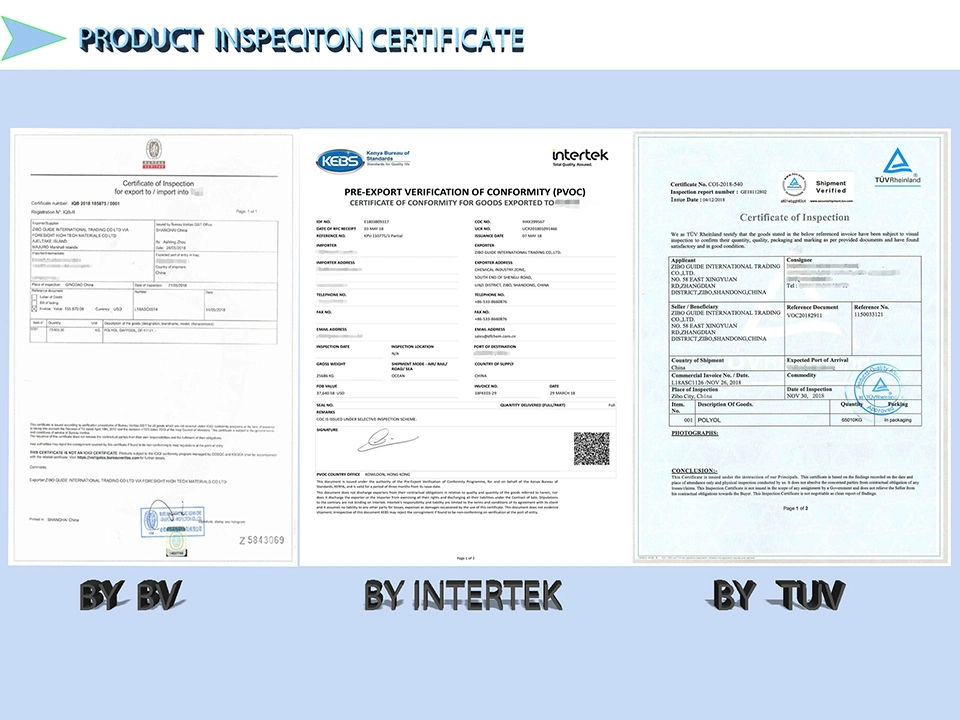
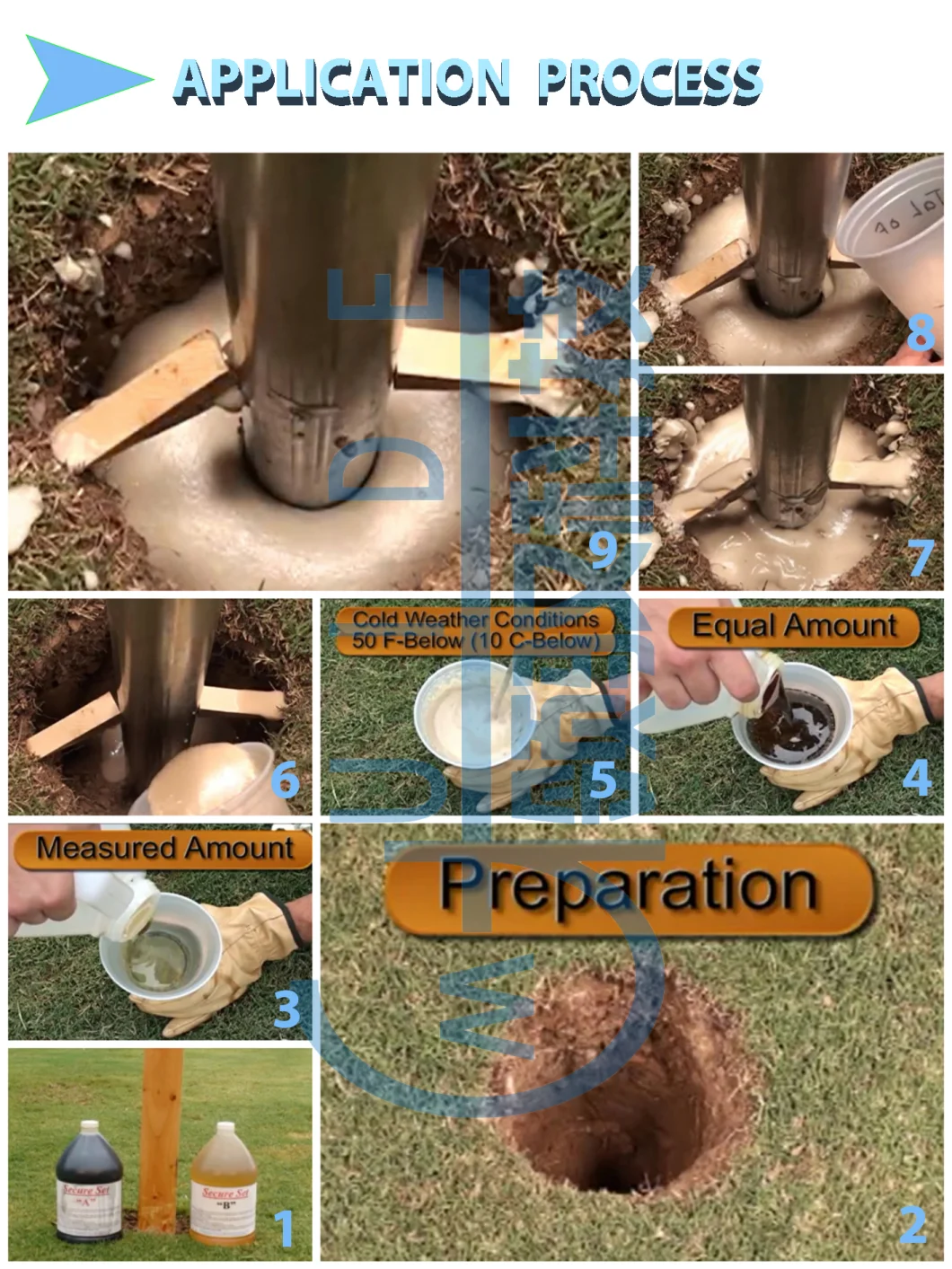